The construction industry relies heavily on large, expensive machinery such as excavators, loaders, dumpers, and cranes. Managing such a fleet is challenging, especially when it comes to fuel expenses, maintenance costs, and ensuring optimal vehicle utilization. Even a small oversight in fleet management can lead to excessive fuel wastage, increased downtime, and higher operational costs.
Challenges
Our client, a leading construction company managing a fleet of over 500 heavy-duty vehicles, faced multiple operational challenges:
- High Fuel Consumption & Wastage: Fuel expenses accounted for a significant portion of the operating costs, with concerns about excessive consumption, fuel theft, and inefficiencies.
- Unexpected Maintenance Costs: Without real-time tracking of engine parameters, fleet managers were unaware of early warning signs of engine issues, leading to high servicing costs.
- Unplanned Downtime & Delays: Unscheduled breakdowns caused project delays and increased costs due to machine unavailability.
- Lack of Visibility into Fleet Operations: The client had no real-time insights into vehicle performance, fuel efficiency, and driver behavior, making it difficult to optimize operations.
Solution: SIMHA Smart Fleet with CAN-Based Telematics
To address these challenges, the client implemented SIMHA Smart Fleet, a CAN-enabled telematics solution that provided end-to-end visibility into fleet operations. The key features of the solution included:
- Real-Time Engine Monitoring: The CAN-based SIMHA Smart Fleet device collected engine parameters such as fuel consumption, engine temperature, RPM, and oil pressure, alerting the fleet manager whenever a parameter exceeded safe thresholds.
- Fuel Efficiency Tracking & Wastage Reduction: By monitoring real-time fuel consumption per kilometer and per ton, fleet managers identified inefficient vehicles and reduced fuel wastage from excessive idling and harsh driving.
- Predictive Maintenance & Cost Control: The system flagged early signs of mechanical issues, allowing proactive servicing before minor issues escalated into costly repairs.
- Fleet Expense Management: The platform allowed fleet managers to log and track servicing costs, fuel top-ups, and other expenses, enabling cost analysis per vehicle, per trip, and per ton.
- Automated Alerts & Notifications: The system notified fleet managers about excessive fuel consumption, harsh braking, overloading, and any anomalies in engine performance.
- Driver Behavior Analysis: Harsh acceleration, sudden braking, and excessive idling were monitored to improve driver performance and reduce wear and tear on vehicles.
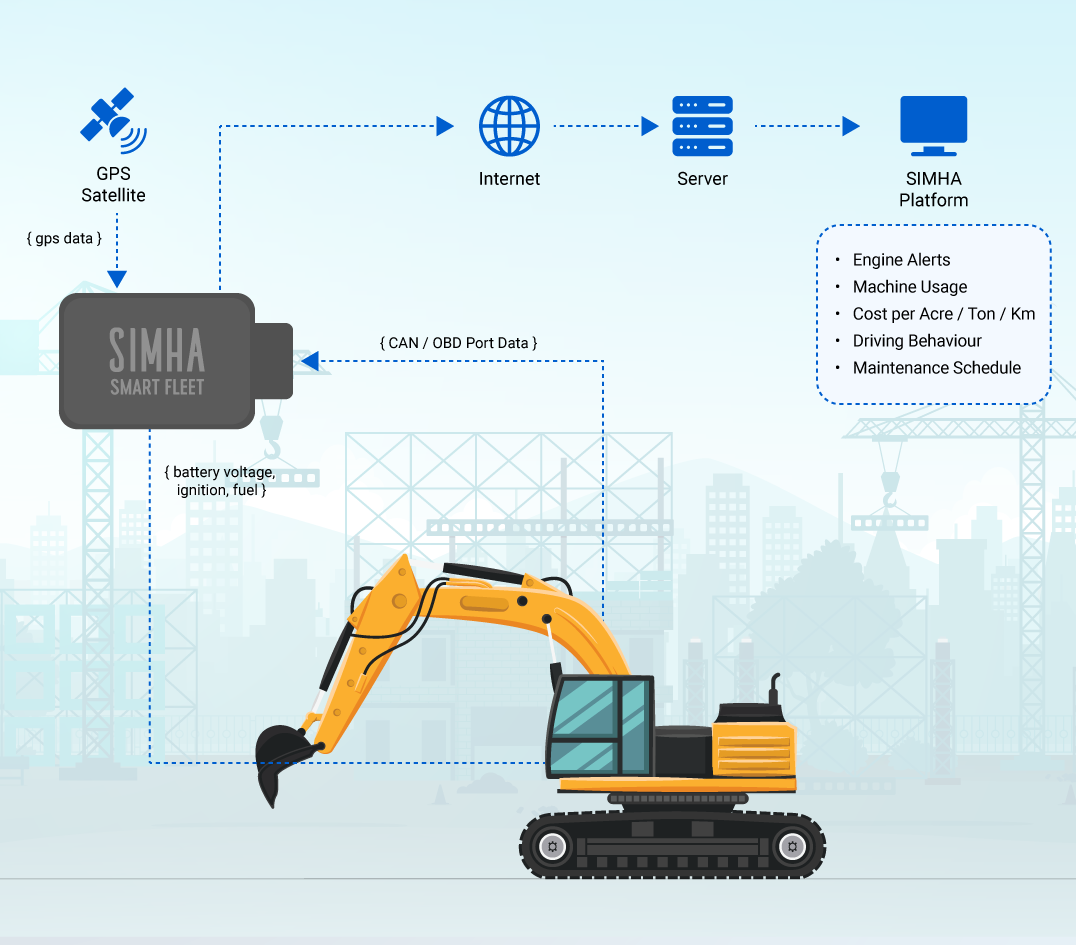
Key Benefits
By integrating SIMHA Smart Fleet, the construction company achieved remarkable improvements in fleet efficiency and cost savings:
- Up to 15% Reduction in Fuel Costs: Optimized fuel usage and reduced wastage through real-time monitoring.
- 30% Decrease in Unplanned Maintenance Expenses: Predictive alerts helped the company service vehicles before breakdowns occurred.
- Enhanced Fleet Utilization & Productivity: Real-time insights allowed better allocation of vehicles to projects, minimizing downtime.
- Improved Safety & Compliance: Monitoring engine health and driver behavior ensured better safety standards and compliance with maintenance protocols.
- Accurate Cost Metrics for Decision-Making: The company gained visibility into fuel costs per trip, maintenance costs per vehicle, and revenue per machine, enabling better financial planning.